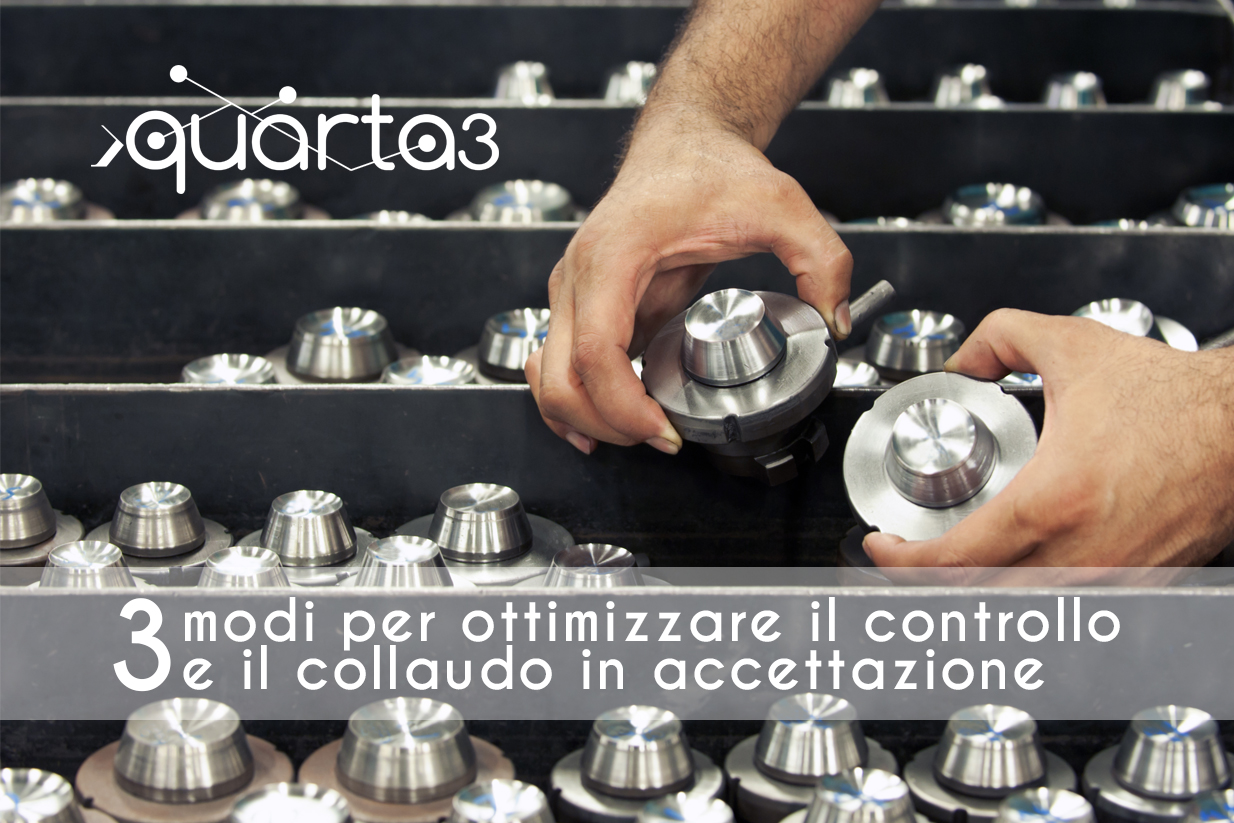
Nell’epoca della Industria 4.0 abbiamo visto come la gestione della qualità non possa più essere considerata in modo analogo a quanto succedeva prima della quarta rivoluzione industriale.
I controlli di qualità sono di fatto la “ratio” stessa del modo di funzionamento delle macchine. Questo avviene in quanto le macchine sono in comunicazione tra di loro e non è ammissibile che una di esse passi alla propria vicina un’informazione sbagliata o un dato che già può essere riconosciuto come fuori dai parametri di qualità.
Per questo si tende a parlare di Quality 4.0, in quanto la Qualità tende ad incorporare in tutto o almeno in parte i concetti cibernetici e di processo che fanno capo alle trasformazioni portate all’industria dai collegamenti di rete e logici tra macchine e computer.
Cosa fa eccezione rispetto a questo scenario? Sicuramente tutti gli ambiti in cui le attività avvengono con un limitato controllo da parte delle macchine e in particolar modo le attività di controllo e di collaudo in fase di accettazione di merci da fornitori. Nonostante che una parte di tali attività possa essere automatizzata, rimangono grandi flussi di merci in arrivo verso le aree a più alta meccanizzazione ed informatizzazione che sono ancora soggetti a controlli di fatto manuali.
Esistono modi per ridurre le possibilità di errore in fase di controllo e collaudo, prima che questi errori vadano ad interessare processi di fatto “error-free”? Ecco come fare secondo Blulink:
- Collegare strumenti di misura
tutte le fasi di controllo in cui è possibile inserire strumenti di misura possono rendere il processo manuale molto simile a quanto accade per i processi “machine-to-machine”, riducendo così i margini di errore tramite un invio in tempo reale dei dati agli strumenti applicativi che sono in grado di rilevarne la bontà e di segnalare prontamente gli scostamenti. - Predisporre il controllo in modo da consentire il cosiddetto “Free pass”
Le procedure di controllo non devono necessariamente essere le stesse per tutti i materiali e possono essere invece differenziate in modo da focalizzarsi sui componenti che hanno generato più problemi in passato, consentendo così una sorta di “autocertificazione” per gli altri, che possono comunque essere soggetti a controlli più laschi ma non inesistenti; questa gestione può e deve chiaramente essere dinamica e aggiornabile sulla base dei risultati dei controlli in tempo reale; - Integrare la fase di controllo con i sistemi CAD ed i sistemi gestionali
Esistono cicli di collaudo e dettagli sulle caratteristiche da controllare che possono essere importati direttamente dai sistemi CAD, in questo modo riducendo i tempi di implementazione dei controlli stessi ma soprattutto eliminando quasi completamente i rischi di errore.
In sintesi, il collegamento di strumenti di misura, quando viene collegata ad almeno una delle altre due modalità di ottimizzazione sopra esposte, è un’attività particolarmente proficua e numerosi tool esistono sia a livello di hardware (come i calibri digitali) sia a livello di software per raccogliere il dato dal campo e integrarlo con le misure esatte che il pezzo deve avere, secondo il disegno CAD digitale tridimensionale che presiede tutto il ciclo di controllo.
Le misure così effettuate possono quindi poi essere trasferite ad un gestionale che si occupa di verificare gli scarti esatti tra il pezzo o il prodotto progettato e quanto ricevuto dal fornitore, allo scopo di poter disporre di un processo di controllo preciso e statisticamente rilevante. Il processo di controllo può evidentemente dare il via all’accettazione automatica, alla marcatura della misura rispetto alla tolleranza o al rigetto del pezzo qualora fuori tolleranza.
Il dato di non conformità, sia all’interno che al di fuori della tolleranza, può poi essere sottoposto ad un controllo percentuale in modo da evitare che i pezzi difformi rispetto alle misure desiderate siano eccedenti una certa soglia. Gli stessi dati possono evidentemente essere trasmessi in tempo reale non solo ai fornitori per la loro analisi ma anche ad altri partner industriali che ne possono necessitare per integrare i loro processi produttivi così come alle macchine impegnate negli stessi, per realizzare un vero e proprio processo Quality 4.0 praticamente “Error-free”…!
L’insieme di queste modalità di messa in opera delle attività di controllo e collaudo in accettazione può rendere questi step molto simili a quanto avviene in una trasmissione “perfetta” di dati tra macchina e macchina. Ovviamente si tratta di previsioni che richiedono strumenti software come quelli di Blulink ed è per questo che i prodotti Software Quarta sono stati realizzati e vengono oggi utilizzati da migliaia di aziende nel mondo.
Contattaci per avere informazioni di dettaglio !